La séance de recrutement aura lieu le 28 septembre 2023 à 19h dans le CO1. Si rejoindre un de nos projets ou un de nos projets de semestre vous intéresse nous vous conseillons fortement d’assister à cet évènement. Vous aurez l’occasion de rencontrer les personnes à la tête des différents projets de l’association. Ceux-ci présenteront également plus en détails chaque projet et le travail attendu
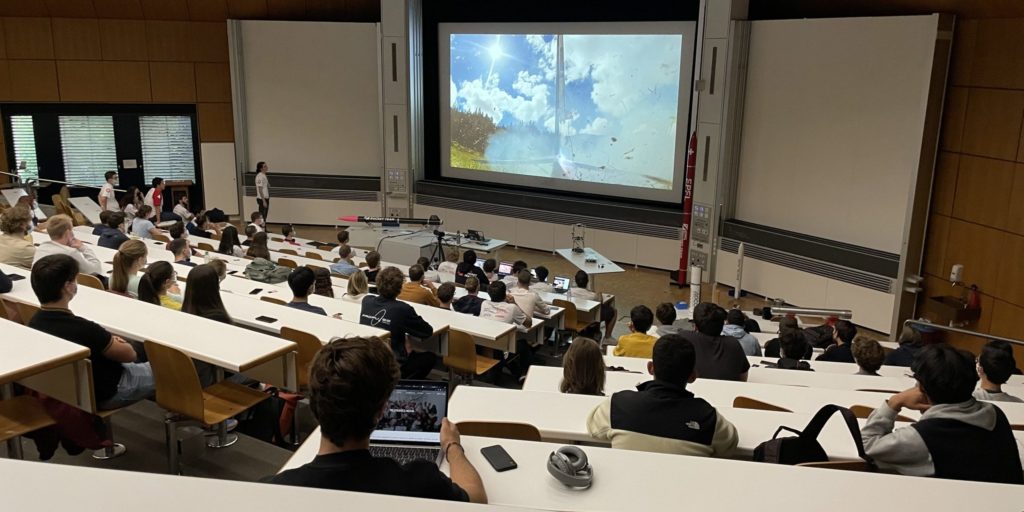
Projets de semestre
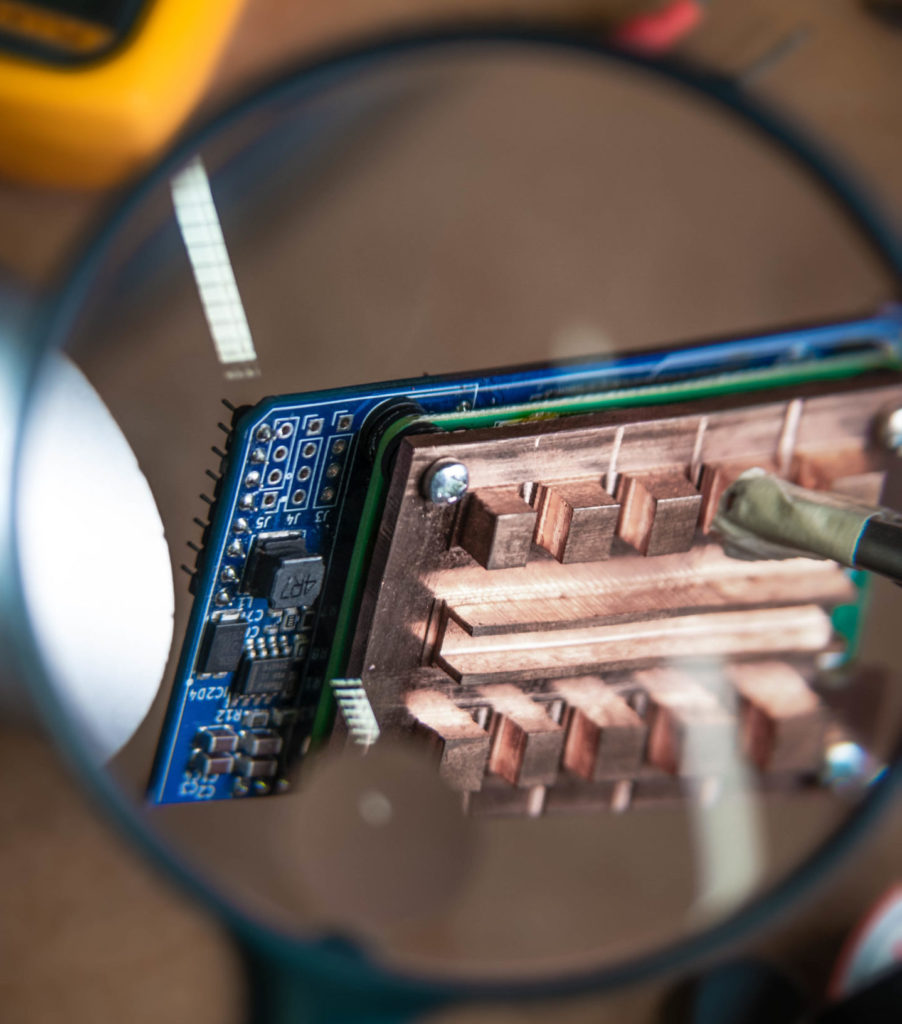
Si vous êtes intéressés par les projets de semestre que nous avons à proposer, vous trouverez la liste et la description de chacun d’entre eux dans le lien qui suit. Les projets de semestre proposés concernent nos projets de recherche (Icarus et Hypérion) ainsi que le projet de compétition.
MANAGEMENT
Notre équipe de sponsoring se charge de trouver de nouveaux sponsors tout en développant la relation que nous entretenons avec nos partenaires actuels. Cela nécessite de bonnes compétences en relations humaines et un certain sens de la vente et de la négociation. Nous recherchons également des étudiants, expérimentés ou non, motivés à trouver de nouvelles idées pour rendre nos prestations de sponsoring aussi attractives que possible.
Compétences souhaitées : Maîtrise du français et de l’anglais, une aisance en allemand serait un vrai plus. Toutes sections de l’EPFL, UNIL, HEC ou HEIG-VD sont les bienvenus.
Notre équipe de communication est responsable de la promotion de l’association que ce soit sur nos réseaux sociaux, sur le campus de l’EPFL ou dans la presse. Elle est composée de rédacteurs, d’un community manager mais aussi de photographes, de vidéographes et d’un webmaster.
Compétences souhaitées pour l’équipe rédactionnelle : Français impeccable, bonnes connaissances de l’anglais, et sens du relationnel. Bonnes capacités de vulgarisation. Toutes sections de l’EPFL, UNIL et SAWI bienvenus.
Compétences souhaitées pour l’équipe visuelle : Sens de l’image, compétences en edit et/ou en montage. Toutes sections de l’EPFL, ECAL, CEPV et autres écoles/universités bienvenus.
Notre équipe de logistique se charge d’organiser nos événements, nos voyages et gère de la logistique courante. Il faut être une personne organisée ayant le permis de voiture. C’est une occasion d’apprendre la gestion et développer des compétences transversales.
Compétences souhaitées : Toutes sections de l’EPFL, UNIL, HEC ou HEIG-VD bienvenus. Permis de voiture nécessaire.
Notre équipe de ressources humaines se charge d’organiser nos événements avec l’équipe Logistique, gère les entretiens avec les nouveaux membres, planifie des évènements pour vivifier l’association et gère les accès à nos différents services. Il faut être à l’aise à l’oral, organisé et à l’écoute des autres membres.
Compétences souhaitées : Toutes sections de l’EPFL, UNIL, HEC ou HEIG-VD bienvenus.
Vice-présidence
Le rôle de Vice-président·e Communication est de gérer l’équipe communication, il vient avec des responsabilités ainsi qu’une place au comité. Il faut savoir être organisé, déléguer du travail et surtout travailler en équipe. Il faut également avoir un bon sens de la mise en page pour pouvoir publier sur nos réseaux sociaux.
Compétences souhaitées : Français impeccable, bonnes connaissances de l’anglais, et sens du relationnel. Bonnes capacités de vulgarisation. Toutes sections de l’EPFL, UNIL et SAWI bienvenus.
Le rôle de Vice-président·e Logistique est de gérer l’équipe logistique , il vient avec des responsabilités ainsi qu’une place au comité. Il faut avoir une vision d’ensemble de l’association et des évènements qui s’y préparent ainsi que savoir être organisé, déléguer du travail et travailler en équipe.
Compétences souhaitées : Toutes sections de l’EPFL, UNIL, HEC ou HEIG-VD bienvenus. Permis de voiture nécessaire.
Le rôle de Vice-président·e Ressources Humaines est de gérer l’équipe RH, il vient avec des responsabilités ainsi qu’une place au comité. Il faut avoir une vision d’ensemble des évènments qui se préparent dans l’association, savoir être organisé, déléguer du travail et travailler en équipe. Il faut également être à l’écoute des membres de l’association et pouvoir proposer des solutions au comité.
Compétences souhaitées : Toutes sections de l’EPFL, UNIL, HEC ou HEIG-VD bienvenus.
PROJET DE COMPETITON
EuRoC 2023
Avionics
L’avionics permet à le fusée de récolter des informations sur la fusée (vitesse, position, accélération, etc) et les envoyer à l’équipe au sol.
L’avionics est aussi responsable de déclencher les différents évènements liés au parachute au bon moment. Enfin, dépendant du moteur utilisé, il peut agir comme un intermédiaire entre le système de propulsion et la station au sol.
Available Roles:
Le sous-système Avionics est en charge du design des éléctroniques et du software de la fusée. Pour ce rôle nous cherchons un ingénieur hardware.
Responsabilités:
- Design et améliorer les PCB avionics déjà existants.
- Manufacturer, prévoir et tester les PCBs.
- Se coordonner avec les autres membres de l’équipe hardware
- Créer et mettre à jour la documentation de votre travail.
- Assiter et préparer des slides pour la réunion hebdomadaire.
De l’expérience dans les points suivants sont un plus:
- PCB Design
- Communication protocols
- Electronics
A general idea of the years unfolding:
- [S1-W4]: Start of the pcb design
- [S1-W11]: Preliminary design review
- [S2-W1]: Start of the pcb manufacturing
- [S2-W8]: Critical design review
- [End of S2+Summer until EuRoC]: Testing and rocket integration
The Avionics subsystem is in charge of the design of the electronics and the software of the rocket. To be able to communicate with the ground, we are in need of an RF engineer.
Responsibilities:
- Design and manufacture antennas for the rocket.
- Design and manufacture of RF circuits.
- Coordinate with the other avionics members in charge of the hardware.
- Update and create the documentation for your work.
- Attend and prepare slides for the weekly meetings.
Experience in the following is a plus:
- Antenna design
- Radio-frequency engineering
- PCB design
A general idea of the years unfolding:
- [S1-W4]: Start of the project
- [S1-W11]: Preliminary design review
- [S2-W8]: Critical design review
- [End of S2+Summer until EuRoC]: Testing and rocket integration
The Avionics subsystem is in charge of the design of the electronics and the software of the rocket. In this context, we are looking for a software engineer.
Responsibilities:
- Optimize and update the current software.
- Coordinate with the other members also in charge of the software.
- Update and create the documentation for your work.
- Attend and prepare slides for the weekly meetings.
Experience in the following is a plus:
- Embedded systems
- C/C++
A general idea of the years unfolding:
- [S1-W4]: Start of the project
- [S1-W11]: Preliminary design review
- [S2-W8]: Critical design review
- [End of S2+Summer until EuRoC]: Testing
The Avionics subsystem is in charge of the design of the electronics and the software of the rocket. To be able to fit the hardware in the rocket, we are looking for a mechanical engineer to design the avionics bay.
Responsibilities:
- Coordinate with the Structure subsystem to ensure compatibility with the rocket airframe.
- Coordinate with the Recovery and Propulsion Subsystem in regards to cable management.
- Coordinate with the other avionics members in charge of the hardware.
- Update and create the documentation for your work.
- Attend and prepare slides for the weekly meetings.
Experience in the following is a plus:
- CAD
A general idea of the years unfolding:
- [S1-W4]: Start of the project
- [S1-W11]: Preliminary design review
- [S2-W8]: Critical design review
- [End of S2+Summer until EuRoC]: Testing and rocket integration
The Avionics subsystem is in charge of the design of the electronics and the software of the rocket. In this context, we are looking for a cable harness engineer to manage all cables going to and from the Avionics module.
Responsibilities:
- Design a cable harness solution for the Avionics subsystem.
- Interface with the Propulsion and Recovery subsystem to account for their needs.
- Coordinate with the other members also in charge of the Avionics hardware.
- Update and create the documentation for your work.
- Attend and prepare slides for the weekly meetings.
Experience in the following is a plus:
- CAD
- General Electrical knowledge
A general idea of the years unfolding:
- [S1-W4]: Start of the project
- [S1-W11]: Preliminary design review
- [S2-W8]: Critical design review
- [End of S2+Summer until EuRoC] Testing and rocket integration
Recovery
The purpose of the Recovery subsystem is to slow down the rocket’s fall to ensure a safe landing after its ascent.
This is usually done with parachutes, but experimentation is always welcome!
Available Roles:
The Recovery subsystem is in charge of getting the rocket back safely on the ground, usually with a set of two parachutes opened at different times (fast then slow) so that the rocket can touch down safely without drifting too far away. In this context, we are looking for someone to design, manufacture and test our new and improved set of parachutes!
Responsibilities:
- Design the parachute(s) needed to recover the rocket at the competition.
- Manufacture the designed parachutes.
- Design, plan and execute the testing of the parachutes.
- Coordinate with the other members of the Recovery subsystem.
- Update and create the documentation.
- Attend meetings and prepare summaries of work done and ahead.
Experience in the following is a plus:
- General Fluid Dynamics
- Sewing Basics
- CAD
A general idea of the years unfolding:
- [S1-W3]: Start of the project.
- [S1-W9]: Preliminary Design Review.
- [S2-W3]: Critical Design Review.
- [S2-W8]: The system is supposed to be manufactured and ready for testing.
- [End of S2+Summer until EuRoC] Testing, Launch simulation+rocket integration.
The Recovery subsystem is in charge of getting the rocket back safely on the ground, usually with a set of two parachutes opened at different times (fast then slow) so that the rocket can touch down safely without drifting too far away. In this context, we are looking for someone to design, manufacture and test the second event mechanism, to deploy the second and main parachute.
Responsibilities:
- Update the design of the actual second event mechanism.
- Manufacture or plan the manufacture of the mechanism.
- Integrate the mechanism with the whole system, ensuring interfaces.
- Being part of the test campaign for the whole recovery subsystem.
- Update and create the documentation.
- Attend meetings and prepare summaries of work done and ahead.
Experience in the following is a plus:
- General stress theory
- Basics in Electronics
- CAD
A general idea of the years unfolding:
- [S1-W3]: Start of the project.
- [S1-W9]: Preliminary Design Review.
- [S2-W3]: Critical Design Review.
- [S2-W8]: The system is supposed to be manufactured and ready for testing.
- [End of S2+Summer until EuRoC] Testing, Launch simulation+rocket integration.
The Recovery subsystem is in charge of getting the rocket back safely on the ground, usually with a set of two parachutes opened at different times (fast then slow) so that the rocket can touch down safely without drifting too far away. In this context, we are looking for someone to design, assemble and test the different lines linking parachutes and rocket parts together, alongside calculating the necessary swivel and other links between the line and the rigid rocket parts/parachutes.
Responsibilities:
- Design the different lines, the cords between the parachutes and the rocket, for the two parachutes.
- Avoid any issues with the tangle of the different cords of the parachutes.
- Do all the calculations needed to chose the right swivels.
- Being part of the testing phase of the parachutes and of the recovery system.
- Coordinate with the other member also charged of the parachutes and of the structure of the rocket.
- Update and create the documentation.
- Attend meetings and prepare summaries of work done and ahead.
Experience in the following is a plus:
- Practical knowledge
- Sense of dynamical behavior
A general idea of the years unfolding:
- [S1-W3]: Start of the project.
- [S1-W9]: Preliminary Design Review.
- [S2-W3]: Critical Design Review.
- [S2-W8]: The system is supposed to be manufactured and ready for testing.
- [End of S2+Summer until EuRoC] Testing, Launch simulation+rocket integration.
Structures
The Structure Subsystem is in charge of designing and producing the rocket’s fuselage, as well as ensuring that it is capable of surviving mechanical and thermal stresses before, during, and after the flight.
Available Roles:
The Structures subsystem is in charge of the design, simulation and manufacture of all structural elements within the rocket. In particular, the Structures subsystem is in charge of designing, simulating and manufacturing the tanks for the engine. For this purpose, we are looking for an Engineer in charge of the Engine Tanks.
Responsibilities:
- Design the rocket’s tank and end caps.
- Work with propulsion to assure compatibility with their engine.
- Assure the tank’s structural role if a structural tank is chosen.
- Update and create the documentation.
- Attend meetings and prepare summaries of work done and ahead.
Experience in the following is a plus:
- General mechanical engineering knowledge
- Aluminium welding techniques
- Structural and Thermal simulations
- CAD
A general idea of the years unfolding:
- [S1-W4]: Brainstorming start
- [S1-W6]: Design start
- [S1-W11]: Primary design review
- [S2-W1]: Manufacturing start
- [S2-W8]: Critical design review
- [End of S2+Summer until EuRoC]: Manufacturing and testing
The Structures subsystem is in charge of the design, simulation and manufacture of all structural elements within the rocket. In particular, the Structures subsystem is in charge of designing, simulating and manufacturing the Payload Integration Structure, which will all the team to integrate the Payload securely within the rocket. For this purpose, we are looking for an Engineer in charge of the Payload Integration Structure.
Responsibilities:
- Designing the system while taking into accounts the requirements.
- Assuring the structural Integrity of the payload with calculations and simulations.
- Follow the manufacturing process.
- Test the integration of the payload.
- Keep up to date the documentation of the system on the ERT wiki.
- Attend and prepare slides for the weekly meetings.
- Prepare slides for the preliminary and critical design review.
Experience in the following is a plus:
- General mechanical engineering knowledge
- Structural and Thermal simulations
- CAD
A general idea of the years unfolding:
- [S1-W4]: Brainstorming start.
- [S1-W11]: Preliminary design review.
- [S2-W8]: Critical design review.
- [End of S2+Summer until EuRoC]: Manufacturing and testing.
The Structures subsystem is in charge of the design, simulation and manufacture of all structural elements within the rocket. In particular, the Structures subsystem is in charge of designing the internal structural elements as well as the plate that will take the shock of parachute deployment. For this purpose, we are looking for an Engineer in charge of the Internal Coupler and Parachute Shock Plate.
Responsibilities:
- Designing the system while taking into accounts the requirements.
- Assuring with calculations and simulations the viability of the system.
- Consider the interfaces with other subsystems.
- Follow the manufacturing process.
- Keep up to date the documentation of the system on the ERT wiki.
- Attend and prepare slides for the weekly meetings.
- Prepare slides for the preliminary and critical design review.
Experience in the following is a plus:
- General mechanical engineering knowledge
- Structural simulations
- CAD
A general idea of the years unfolding:
- [S1-W4]: Brainstorming start
- [S1-W11]: Preliminary design review
- [S2-W8]: Critical design review
- [End of S2+Summer until EuRoC]: Manufacturing and testing
The Structures subsystem is in charge of the design, simulation and manufacture of all structural elements within the rocket. In particular, the Structures subsystem is in charge of designing and manufacturing the fins and integrate them on a fincan for the rocket. For this purpose, we are looking for an Engineer in charge of the Fincan.
Responsibilities:
- Design the rocket’s boattail and fincan coupler.
- Manufacture the boattail and overall fincan.
- Work with structure’s composite team.
- Assure the aerodynamics target of the rocket.
- Update and create the documentation on your work.
- Attend meetings and prepare summaries of work done and ahead.
Experience in the following is a plus:
- General mechanical engineering knowledge
- Structural and CFD simulations
- CAD
A general idea of the years unfolding:
- [S1-W4]: Brainstorming start.
- [S1-W11]: Preliminary design review.
- [S2-W8]: Critical design review.
- [End of S2+Summer until EuRoC]: Manufacturing and testing.
The Structures subsystem is in charge of the design, simulation and manufacture of all structural elements within the rocket. In particular, the Structures subsystem is in charge of integrating the new engine provided by the propulsion subsystem inside the airframe. For this purpose, we are looking for an Engineer in charge of the Engine Integration.
Responsibilities:
- Design the rocket’s engine integration structure and interface parts.
- Manufacture the EIS and interface parts.
- Work with structure’s fincan team and with the propulsion team.
- Assure the engine’s thrust transmission to the airframe.
- Assure the accessibility of the plumbing by the propulsion team during assembly.
- Attend meetings and prepare summaries of work done and ahead.
Experience in the following is a plus:
- General mechanical engineering knowledge
- Structural simulations
- CAD
A general idea of the years unfolding:
- [S1-W4]: Brainstorming start
- [S1-W6]: Design start
- [S1-W11]: Primary design review
- [S2-W1]: Manufacturing start
- [S2-W8]: Critical design review
- [End of S2+Summer until EuRoC]: Manufacturing and testing
The Structures subsystem is in charge of the design, simulation and manufacture of all structural elements within the rocket. In particular, the Structures subsystem is in charge of designing and simulating the airframe, fins and nosecone using composite materials. For this purpose, we are looking for an Engineer in charge of composites.
Responsibilities:
- Design the rocket’s fins, fuselage and nosecone using composite materials.
- Simulate the composite’s behaviour under thermal and structural loads.
- Design and follow the part’s manufacturing.
- Assure radio transparency for radio communication on the part of the fuselage reserved for the Avionics module.
- Attend meetings and prepare summaries of work done and ahead.
Experience in the following is a plus:
- General mechanical engineering knowledge
- Experience with composite materials
- Structural simulations using composites
- CAD
A general idea of the years unfolding:
- [S1-W4]: Brainstorming start
- [S1-W6]: Design start
- [S1-W11]: Primary design review
- [S2-W1]: Manufacturing start
- [S2-W8]: Critical design review
- [End of S2+Summer until EuRoC]: Manufacturing and testing
The Structures subsystem is in charge of the design, simulation and manufacture of all structural elements within the rocket. In particular, the Structures subsystem is in charge of designing, simulating and manufacturing the Separation Mechanism. This mechanism allows the rocket to separate on demand to let the first parachute out.
Responsibilities:
- Update and upgrade the separation mechanism that has been developed over the past few years.
- Coordinate the design with the Recovery team to ensure interfaces.
- Plan and carry over the manufacture of the system.
- Testing of the mechanism under nominal and off-nominal scenarios.
- Update and create the documentation.
- Attend meetings and prepare summaries of work done and ahead.
Experience in the following is a plus:
- General mechanical theory
- CAD
A general idea of the years unfolding:
- [S1-W3]: Start of the project.
- [S1-W9]: Preliminary Design Review.
- [S2-W3]: Critical Design Review.
- [S2-W8]: The system is supposed to be manufactured and ready for testing.
- [End of S2+Summer until EuRoC] Testing, Launch simulation+rocket integration.
Propulsion
The Propulsion subsystem is where the magic happens. Fire comes out on one end, pushing the rocket towards its objective.
This year, the team is aiming to fly its very first Liquid engine with Ethanol as fuel and Nitrous Oxide as the oxidizer.
Available Roles:
The propulsion subsystem is responsible for developing and integrating a 1kN bi-liquid rocket engine (Demo-A2) for the competition rocket, based on previous work done by the Hyperion project.
The engine design engineer will be responsible for the adaptation of the existing test engine Demo-A1 into a flyable version. The 2 main challenges are the ability of the Demo-A2 engine to sustain longer burn time (between 5 and 15 seconds, TBD) and the reduction of mass. As the internal design is already done, the focus will be put on external geometry, mainly using mechanical and more importantly thermal simulations.
The engine should be as simple as possible (a.k.a no regenerative cooling). Possible solutions are (but not restricted to): ablative chamber/nozzle, ablative internal insulation, film cooling, …
Responsibilities:
- Mechanical design and simulations of the engine.
- Thermal simulations of the engine.
- Pressure testing of the engine.
- Cold Flow testing of the engine.
- Hotfire testing of the engine.
- Update and create the documentation for your work.
- Attend meetings and prepare summaries of work done and ahead.
Experience in the following is a plus:
- Thermal and mechanical simulations
- CAD
A general idea of the years unfolding:
- [S1-W1-8] Problem analysis, solutions catalog.
- [S1-W8-14] Solution choice and design for manufacturing.
- [S2-W1-6] Manufacturing, test.
- [S2-W4-EuRoC] Hotfire test, optimisation.
The propulsion subsystem is responsible for developing and integrating a 1kN bi-liquid rocket engine (Demo-A2) for the competition rocket, based on previous work done by the Hyperion project.
The plumbing integration engineer is responsible for the design and integration of the internal plumbing of the competition rocket rocket needed to operate a bi-liquid engine. The plumbing system shall be able to fill, purge, vent and pressurize the tanks, and to transfer propellant from the tanks to the combustion chamber
Responsibilities:
- Valve selection for the engine.
- Plumbing design that can be integrated in the restricted volume of the rocket.
- Manufacture and integration of the plumbing and the valves in the rocket.
- Testing of the subassemblies and of the final assembly.
- Update and create the documentation for your work.
- Attend meetings and prepare summaries of work done and ahead.
Experience in the following is a plus:
- CAD
- High-pressure plumbing knowledge
- Good spatial representation
A general idea of the years unfolding:
- [S1-W1-10]: Valve selection, plumbing concept.
- [S1-W1-14]: Components order, tests.
- [S2-W1-6]: Rocket integration, tests.
- [S2-W6-EuRoC]: Hotfire tests, optimisation.
Payload
The Payload is the sub-system in charge of imagining, developing and integrating the scientific experiment powered by the rocket.
This years experiment is not yet chosen, give us your ideas!
Available Roles:
Coming…
Ground Segment
The Ground Segment subsystem is in charge of all ground operations before, during and after the launch.
This includes, among others, the management of a Ground Station equipped with radios and antennas, as well as a 9m tall Launch Rail.
Available Roles:
No roles for this year!
Flight Dynamics
The Flight Dynamics subsystem is in charge of all simulations related to the rocket in general.
It is in particular flight simulations with commercial tools as well as with home-made simulators, and fluidic studies on the aerodynamics of the rocket.
Simulations performed are, amongst others, predictions for the rockets trajectory, statistical drop-zones for nominal and off-nominal trajectories, aerodynamics/thermal/fluid analysis on the airflow around the rocket at various velocities.
Available Roles:
The Flight Dynamics subsystem is in charge of the rocket’s aerodynamic and flight performances. In this context, we are looking for a supersonic wind tunnel engineer.
The person filling this role will work on the design of a small scale supersonic wind tunnel. Considering the rareness of such infrastructure in Switzerland and in Europe, the association decided to build one in-house. A first feasibility study was realized during the Spring semester 2022. However, further improvements should be realized before beginning the manufacturing phase. Wind tunnels are used to simulate aerodynamic effects that would affect an object. To do so, a flow of gas is accelerated from a rest state to a velocity simulating the one the object will experiment during its movement. Such a tunnel could give invaluable results for the development of future rockets.
Responsibilities:
- Progress on the design and development of the Supersonic Windtunnel.
- Update and create the documentation for your work.
- Attend meetings and prepare summaries of work done and ahead.
Experience in the following is a plus:
- Fluid Mechanics (in particular compressible flows)
- Physics (Optics, in particular Schlieren imaging)
A general idea of the years unfolding:
- [S1-W3]: Reading what has been done in previous projects.
- [S1-W14]: Second iteration of the design.
- [S2]: Improvement of the design.
The Flight Dynamics subsystem is in charge of the rocket’s aerodynamic and flight performances. In this context, we are looking for a flight simulator engineer.
The person filling this role will work on the in-house flight simulator developed by the EPFL Rocket Team. The results of these simulations are essential to validate our design and ensure proper flight characteristics. At the moment, external simulators are used. However, they all have their pros and cons and, although useful, they do not provide as much freedom in their use as a simulator developed internally. For this reason, the association decided to develop its own flight simulator. A certain basis is existent but further development is still needed for the simulator to perform efficiently. We hope to use it as principal support for the simulations at the 2023 competition.
Responsibilities:
- Progress on the design and development of the teams Flight Simulator.
- Update and create the documentation for your work.
- Attend meetings and prepare summaries of work done and ahead.
Experience in the following is a plus:
- Programming (ideally Matlab)
- Data analysis and interpretation
- Physics
A general idea of the years unfolding:
- [S1]: Further develop the current in-house simulator.
- [S2]: Validate its results with experimental Data and cross-check with other external flight simulators.
The Flight Dynamics subsystem is in charge of the rocket’s aerodynamic and flight performances. In this context, we are looking for a flight simulations engineer.
The person filling this role will work on simulating the flight of the rocket under various scenarios as well as perform sensitivity analyses for the rocket taking part in the 2023 competition. This person will mainly use flight simulators but should be able to analyze and interpret the results. These simulations are crucial and used to determine and validate the design of the rocket. This person will, then, be a contact for other subsystems (Propulsion, Structure, …) should they have precise questions on the impact of different requirements.
Responsibilities:
- Perform the required flight simulations.
- Update and create the documentation for your work.
- Attend meetings and prepare summaries of work done and ahead.
Experience in the following is a plus:
- Programming (ideally Matlab)
- Data analysis and interpretation
- Good interpersonal skills
A general idea of the years unfolding:
- [S1]: Determination of the general requirements for the rocket, sensitivity analyses.
- [S2]: Simulations to support the adopted design, adapt simulations to changes in design.
The Flight Dynamics subsystem is in charge of the rocket’s aerodynamic and flight performances. In this context, we are looking for an aerodynamic simulations engineer.
The person filling this role will work on Computational Fluid Dynamics (CFD) simulations for the rocket taking part in the 2023 competition. The results of such simulations are essential for the team as they guarantee that the rocket’s different components exposed to the external airflow produce as little drag as possible, or in other words, to ensure that the rocket is as aerodynamic as possible for the speed regime it will be flying. This person will also act as a consultant for other subsystems, whenever the aerodynamic performance of a certain airframe component needs to be determined and/or improved. Indeed, launch windows are limited in Switzerland. As a result, it is critical to ensure that the result of the simulations are as physically accurate as possible to be able to make the most of the authorized launches.
Responsibilities:
- Perform the required simulations when inquired by other subsystems.
- Update and create the documentation for your work.
- Attend meetings and prepare summaries of work done and ahead.
Experience in the following is a plus:
- Fluid mechanics (in particular aerodynamics)
- CFD simulations (ideally ANSYS Fluent)
- Good interpersonal skills
A general idea of the years unfolding:
- [S1]: Determination of the shape of aerostructure components.
- [S2]: Simulations to support the adopted design.
The Flight Dynamics subsystem is in charge of the rocket’s aerodynamic and flight performances. In this context, we are looking for an aerodynamics engineer.
The person taking this role will work on the development of active aerodynamics (or mechanisms providing some degrees of active control) for this year’s rocket. In the competition, more points are awarded to rockets being capable to reach their altitude’s category as accurately as possible. For this reason, active control of the rocket would be game changing and represent a significant step forward for the team.
Responsibilities:
- Design a mechanism to achieve a set of requirements.
- Design a manufacturing method for such a mechanism.
- Manufacture the mechanism.
- Test and integrate the mechanism within a launch vehicle.
- Update and create the documentation for your work.
- Attend meetings and prepare summaries of work done and ahead.
Experience in the following is a plus:
- Fluid mechanics (in particular aerodynamics)
- CFD simulations (ideally ANSYS Fluent)
- Mechanical design
- CAD
A general idea of the years unfolding:
- [S1]: Feasibility study, quantify advantages provided by proposed elements.
- [S2]: Eventually manufacture and implement elements of interest.
PROJETS DE RECHERCHE
ICARUS
Le projet Icarus comporte une équipe, constituée de quelques étudiants et entièrement consacrée au développement et à la recherche autour des algorithmes de Guidance, Navigation et Contrôle (GNC) ainsi que du simulateur pour tester ces algorithmes.
Cette année, cette équipe, est principalement dirigée par le laboratoire d’automatique avec les 3 projets de semestres associés. Si tu es motivé mais que tu ne souhaites pas faire un projet crédité, n’hésite pas à nous envoyer un mail à icarus@epflrocketteam.ch
PROJET DISPONIBLES
- Robust touchdown control for a thrust-vector-controlled rocket
- Descent planning for a thrust-vector-controlled rocket
- Online controller adaptation for a thrust-vector-controlled rocket
Le projet ICARUS développe sa toute première fusée de type Hopper permettant d’etre stabilisée en orientant la poussée du moteur et visant a atterrir à la verticale. Pour cela, un module de gimbal permet de rediriger la poussée selon deux degrés de liberté a été conçu. L’objectif est désormais d’affiner le design et de le manufacturer afin de le tester. Dans l’idéal, une petite équipe de 2 étudiants ayant des connaissances pratiques en mécanique et électronique serait parfait pour travailler sur ce module.
Il est également possible d’y travailler dans le cadre d’un projet de semestre.
ROLES DISPONIBLES
Role: Membre de l’équipe Hopper _ Gimbal
Description: En tant que membre de l’équipe, vous participerez à la manufacture, tests, et itération du design.
Profil/Compétences: CAD (Solidworks), Experiences préalables en codage et dans des projets pratiques préférées.
L’objectif est de réussir les premiers vols à l’été prochain !
Le projet ICARUS développe sa toute première fusée de type Hopper permettant d’etre stabilisée en orientant la poussée du moteur et visant a atterrir à la verticale. Pour cela, un module de jambe permettant de garantir la stabilité au sol et d’amortir l’impact a été conçu. L’objectif est désormais de manufacturer un prototype à échelle réduite et de le tester afin d’affiner le design final. Dans l’idéal, une petite équipe de 2 étudiants ayant des connaissances pratiques en mécanique et électronique serait parfait pour travailler sur ce module.
Il est également possible d’y travailler dans le cadre d’un projet de semestre.
ROLES DISPONIBLES
Role: Membre de l’équipe Hopper _ Legs
Description: En tant que membre de l’équipe, vous participerez à la manufacture, tests, et itération du design.
Profil/Compétences: CAD (Solidworks), FEM Simulation (ANSYS), Experiences préalables dans des projets pratiques préférées.
L’objectif est de réussir les premiers vols à l’été prochain !
Le projet ICARUS développe sa toute première fusée de type Hopper permettant d’etre stabilisée en orientant la poussée du moteur et visant a atterrir à la verticale. Pour cela, un module de gimbal et un module de jambe d’atterissage ont été conçu. L’objectif est désormais d’affiner le design de la structure de la fusée et l’intégration de l’avionique puis de la manufacturer afin de la tester. Dans l’idéal, une petite équipe de 2-4 étudiants ayant des connaissances pratiques en mécanique et électronique serait parfait pour travailler sur ce module. Il est également possible d’y travailler dans le cadre d’un projet de semestre visant a développer un mécanisme de contrôle du roulis.
ROLES DISPONIBLES
Role: Membre de l’équipe Hopper
Description: En tant que membre de l’équipe, vous participerez à la manufacture, tests, et itération du design.
Profil/Compétences: CAD (Solidworks), Experiences préalables en codage, en électronique et dans des projets pratiques préférées.
L’objectif est de réussir les premiers vols à l’été prochain !
BI-LIQUIDE
Cette section du projet Hyperion s’occupe du design et de la construction d’un moteur utilisant de l’oxygène liquide (LOx) comme oxydant et de l’éthanol comme carburant. Cette classe de moteur intègrera au fur et à mesure plusieurs technologies qui serviront au space-shot, comme du regenerative cooling ou encore des pompes électriques.
Le premier moteur de classe B sera destiné à être utilisé sur un banc de test, et a pour objectif d’être fabriqué en majorité par l’équipe.
ROLES DISPONIBLES
Rôle: Responsable du design du moteur (2)
Description: Dimensionnement et conception des éléments mécanique du moteur, chambre de combustion, tuyère et injecteur. Le design devra être adapté pour une fabrication de type « additive manufacturing ».
Profil/Compétences: MT-RO, GM, connaissances générales sur la gestion des fluides et les composants commerciaux
Rôle: Spécialiste SLM (Printemps 2023) (1)
Description: Responsable de la fabrication du moteur, étude des contraintes de fabrication par Selective Laser Melting, avec la possibilité d’aller dans un atelier pour la fabrication des pièces.
Profil/Compétences: MT-RO, GM, connaissances en fabrication additive métallique et mécanique générale
Rôle: Spécialiste impeller/volute (2)
Description: Responsable de la conception de la partie fluidique des pompes électriques du moteur de classe B, s’appuyant sur les différents travaux effectués jusqu’à présent.
Profil/Compétences: MT-RO, GM, connaissances générales sur la mécanique des fluides et les composants commerciaux, bonne expérience de la CFD ainsi que la CAO
Rôle: Responsable de l’assemblage mécanique des pompes (1)
Description: Assemblage des différents éléments mécaniques des pompes du moteur de classe B, et intégration/interface avec le moteur électrique.
Profil/Compétences: MT-RO, GM, connaissances en mécanique générale et CAO
Rôle: Responsable des joints (1)
Description: Responsable de l’assemblage pour l’étanchéité dynamique de la pompe électrique du moteur de classe B, utilisant des joints labyrinthe autour de l’arbre.
Profil/Compétences: MT-RO, GM, MX connaissances en mécanique générale, mécanique des fluides et CAO
Rôle: Responsable du contrôle de l’électronique de la pompe (1)
Description: Choix des composants électroniques, du moteur électrique et de la partie de puissance des pompes électriques.
Profil/Compétences: EL, MT-RO, connaissances en électronique
Rôle: Responsable des vannes cryogéniques (1)
Description: Adaptation et qualification d’une vanne commerciale d’usage général pour une utilisation avec de l’oxygène liquide cryogénique.
Profil/Compétences: GM, MT-RO, connaissances en mécanique des fluides, mécanique générales et CAO
Un des aspects les plus critiques dans le développement d’un moteur de fusée bi-liquide est l’espace de test. Celui ci doit etre solide, sécurisé, et très fonctionnel pour pouvoir garantir la sécurité des utilisateurs meme en cas de problème majeur sur le moteur.
ROLES DISPONIBLES
Rôle: Responsable du banc de test (3)
Description: Développement d’un banc de test vertical pour un moteur bi-liquide, afin d’être le plus proche de la réalité. L’objectif étant de concevoir et de fabriquer un banc de test solide et remplissant un cahier des charges précis.
Profil/Compétences: MT, GM, Connaissance d’ingénierie générale en mécanique structurelles et/ou en manufacture, CAO.
Rôle: Responsable capteurs et système d’acquisition (DAQ) (2)
Description: Choix des capteurs et intégration sur le banc de test, pour des mesures de poussée, pressions et forces. Calibration des capteurs à partir de leur fiche technique. Gestion du système d’acquisition afin d’exporter les données des tests.
Profil/Compétences: MT, EL, Connaissance d’ingénierie générale et techniques de mesures
Rôle: Responsable vannes et tuyauterie (1)
Description: Responsable de l’intégration de la tuyauterie, des raccords et des vannes sur le banc de test.
Profil/Compétences: MT, GM, Connaissance d’ingénierie générale en mécanique structurelles et/ou en manufacture et/ou mécanique des fluides.
Rôle: Responsable de l’électronique du banc de test (1)
Description: Développement de l’électronique du banc de test du moteur, câblage de l’armoire électrique. Un système d’acquisition vidéo pour l’espace de test sera aussi développé, composé à majorité de composants commerciaux.
Profil/Compétences: MT, EL, Connaissance d’ingénierie générale en électronique ou en systèmes vidéo.
PROJET DE FORMATION
SPACE RACE
Ce projet a pour but de construire une fusée relativement simple en équipe de 5-7 étudiants. Il permet d’apprendre les bases de la fuséologie tout en apprenant à travailler en équipe. Il est adressé aux premières années et éventuellement deuxième année d’EPFL.
Toutes les sections sont les bienvenues.
LANCEZ VOTRE CARRIERE DANS LE SPATIAL - COMPETITION
Gagnez en expérience et en crédibilité
grâce à des projets crédités et en vous formant aux contraintes de l’industrie, tout en obtenant des opportunités de stage et des recommandations.
Rencontrez votre futur employeur
lors de l’un de nos événements où vous aurez l’occasion de discuter avec des sponsors et des partenaires de l’industrie spatiale.
Développez votre réseau
en rencontrant des employés et des entrepreneurs actifs dans le domaine spatial ainsi que des étudiants talentueux provenant de nos projets.
APPRENEZ DANS UN ENVIRONNEMENT SÛR - SPACE RACE
Bénéficiez de l’infrastructure
unique de l’ERT: un atelier vaste et sécurisé, des mentors dévoués et des technologies de pointe pour vous garantir la meilleure expérience d’apprentissage possible.
Rencontrez votre mentor
qui aidera votre équipe tout au long de l’année pour améliorer votre expérience d’apprentissage et pour s’assurer que votre fusée est bien construite, sécurisée et qu’elle volera avec succès.
Obtenez des certifications
liées à l’usinage, la fabrication ou la conception de fusées : vous bénéficierez de plusieurs ateliers et lancements pour les obtenir tout au long de votre année d’apprentissage.
Pas de pression pendant l’année. Vous aurez une petite compétition uniquement pour le plaisir, et vous êtes ici pour apprendre. Mais vous êtes le bienvenu si vous souhaitez rejoindre l’équipe de compétition après votre année de formation.
DEVENEZ UN PIONNIER - DEPARTEMENT DE RECHERCHE
Créez vos innovations
et participez à des défis fous, comme celui de notre projet Icarus : soyez la première équipe étudiante à faire atterrir sa fusée comme SpaceX.
Libérez votre potentiel
en obtenant de l’espace pour tester toutes vos idées géniales, folles et expérimentales sur l’un de nos projets liés aux fusées.
Vous n’êtes pas certain de vouloir participer à un projet pendant toute une année universitaire? Pensez à choisir l’un de nos projets de semestre crédités ! Chaque année, nous proposons de nombreux projets, dans tous les domaines, déjà suivis par des professeurs de l’EPFL. Trouvez le vôtre !